Mechanical - General 2018
Students
Mentors
Date & Time
Location & Author
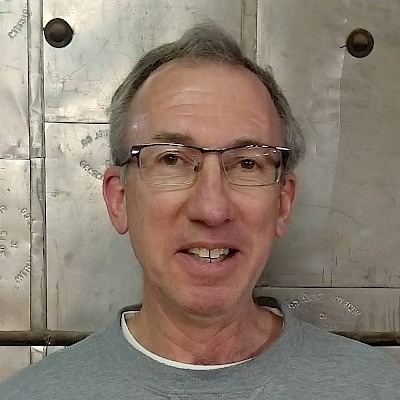
Bob S.
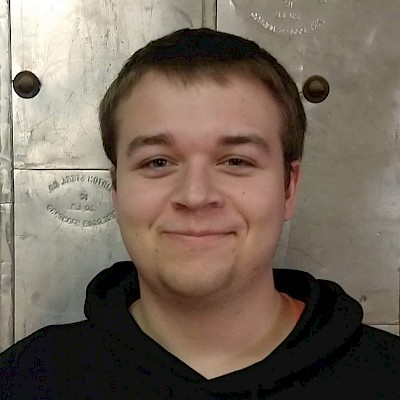
Chris E.
Aquiferland
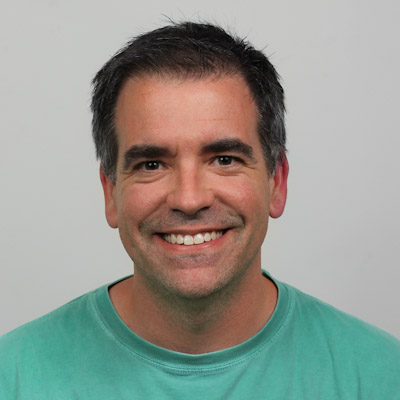
Adam P.
Work Completed
- Lots of testing and analyzing
- Ha and Chris rebuilt the intake using the drive motors and gearboxes from the prototype. They then discovered (around midnight) that the intake doesn't work under some situations and the intake arms need to move out farther than the existing robot structure allows.
- Lots more, see work for next meeting below.
Testing
- 5:1 gearboxes stalled when intaking cube right side up (13x13 dimension) even when there's no pressure to the cylinders --> switched them out for the 10:1 on the prototype
- set working pressure at 30psi, moved carriage up to have more room for the arms to open wider (not restricted by the ramp support beams), removed inner wheels, untwist the ball joint on the cylinders to make the arms open wider
- --> intake super well on the side (11x13)
- still not great w/ 13x13 orientation
- options
- remove front support beam of ramp
- --> allow more room for intake arms to open
- cut longer back channel
- reposition cylinders
- --> tested ramp lifting frisbee with that setup, seems viable and stable enough, will probably add some extra support via corner gussets etc. to be safe
- add another stage of reduction (3:1 to get 30:1)
- switch to 775pros
- change cylinder bore size to something like prototype (3/4" vs 1-1/16" on current design)
- switch motor pulleys from 24-24 to 30-18 for like an extra 1.6 reduction
- remove inner sets of wheels, make notch in arm lexan
Work for Next Meeting
- A large chunk of the front of the robot structure above the drivetrain needs to be removed (pictures to follow) to allow proper operation of the intake.
- Front wheels need to be removed and the gussets holding the vertical tubing in place needs to be removed so the vertical tube can be removed.
- Second stage of elevator needs to be removed to fix the rivet rubbing issue. If you know how to remove the second stage, be at the shop on Sunday.
- The elevator motor is really loose and needs to be tightened, maybe holes tapped....
- Remove drive gearboxes so they can be converted to single speed.
- Elevator
- Second stage of elevator needs to be removed to fix the rivet rubbing issue.
- Remove elevator gearbox, tap 4th hole and remount it
- Electrical
- Finish with plumbing and wiring
- Plan on individually actuating ramps, since raising an unoccupied ramp makes it jump 2 feet in the air.
- Ramps
- Smoke(?) and surgical tubing and spectra line magic that needs to be implemented to have the robot actually rotate the lift cylinders into position and then lift one or two other robots
- Get frisbee bot, weigh it down to 130 lbs and drive it on ramp, actuate it, remove it and repeat like 50 times. Need to prove the cover material will hold up and not break.
- Make bumpers
- duct tape pool noodles to plywood
- carefully fold & cut cloth, attach temporarily to bumpers, fold corners nicely and staple lightly if needed
- mark where numbers go with chalk, or similar
- remove fabric and iron-on the numbers
- staple fabric to plywood (fold corners nicely pls)
- attach L channel to plywood
- drill some holes and make sure mounting/removing with pins is quick/easy
- Testing
- does intake rotate?
- does intake intake?
- does elevator lift smoothly?
- does cube fall out
- actual time for elevator to go full height & back
- time takes for entire lifting routine (get on platform, deploy ramp, other robot climbs on, lift)
-
- Pit Design
- New pit wall for banner, sponsor stuff
- Peg board for tools would be nice
- Robot cart
- fix handle
- add second level again?
- Make awards to give other teams?
- Make buttons?