Electrical & Code 2019
Students
Mentors
Date & Time
Location & Author
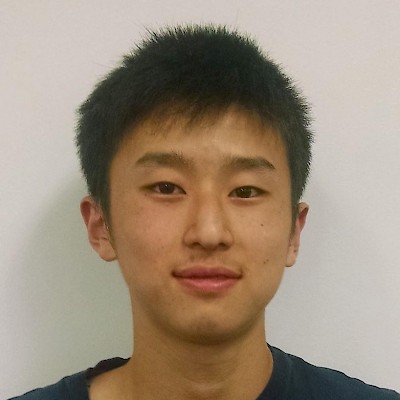
David S.
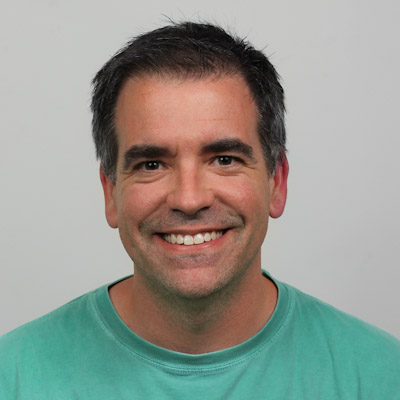
Adam P.
Aquiferland
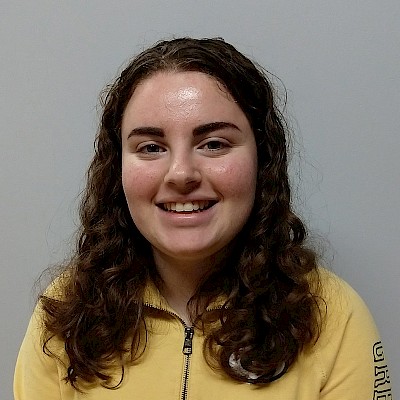
Bryn G.
Work Completed
- Finished control board with just the RoboRIO, PDP (connected via CAN bus), 6 Drivetrain motor controllers (Victor SPs - PWM), VRM, Breaker, and Battery
- It all turned on and worked!
- Connected RoboRIO directly to computer using an ethernet cable instead of dealing with adding a radio and configuring it...
- Adam updated a bunch of stuff on the computer and the RoboRIO and put new firmware on the PDP using the new CTRE platform
- I edited the code to get rid of everything having to do with the gyro, encoders, drive correction, PIDs, etc to run the two gearboxes
- Broke in the two mounted gearboxes for 20 minutes in each direction with a lot of grease
- Thomas & David created the cables for the two encoders for DT1 (5 pin connector using 2 PWM cables)
- One encoder is mounted on top of the gearbox
- Other encoder is mounted on the bottom bc there was some issue with the top mounting holes --> will this be an issue with wiring?
- When I left, Caden was working on the schematic some more
Challenges
- Code had a lot of bugs that needed to be fixed to get the gearboxes driving. It probably would have been quicker to just created a new set of code that would just worry about driving the motors
- Keeping the two driver stations to be EXACTLY the same
Work for Next Meeting
- Figure out the mounting for the limelight --> we want it somewhere on the Hatch side of the robot
- Verify Roborio (gyro, actually) will be close to center of rotation on robot. Rearrange layout accordingly.
- Make list of all the general & subteam specific electrical components on the robot (FRC4096 --> 2018 - 2019 --> Build Season --> Electrical folder --> Electrical components)
- Continue wiring the DT1 once it is done being assembled by mechanical (should be sometime this coming week)
- Keep in mind that we need someplace for...
- The breaker
- The new ethernet switch
- Two PCMs
- Solenoid blocks, etc.
- Continue the schematic for the electrical system using the schematic software stuff --> talk to Malia & Caden about this if you are interested (or maybe eddy)
- Figure out the pneumatics situation
- How many pistons?
- Which pistons can be run together off of one solenoid?
- How many double solenoids will we need then? ... if more than five, we will need another block ... if more than four we need another PCM on the robot
- Will our compressor be strong enough to handle this all?
- Get drivetrain code to work on the debugger (may just need to add the physics and sim files to the code???)
- Build a set-up to run a motor when testing and making prototypes
- Adam bought a 4-AA battery holder with on/off switch. Hook this up and try using it to supply the +5v power to the new motor tester
- Vision
- Now that the gyro is working again, this should be worked on some more...
- Drive robot towards vision target so the target is in view of limelight; then have robot drive to a specified distance and turn to a specified angle from the vision target (using a calibrated position and the tx & ty from the limelight)
- Get Rotate_To_Angle_Limelight command working on Poly again. PID will need tuning.
- Continue learning how to use limelight
- Specifically learn what all of the different values on the network table are and how they can be used
- Continue to look into the Limelight documentations
- Go to specified range from target (check case studies on limelight website & documentation)
- Go to specified range and aim at target (again check case studies)